Quality Assurance
Quality Assurance for the Production of Quality Parts
Flagship has achieved ISO 9001:2015 certification for its Quality Management System, demonstrating our dedication to ongoing quality enhancement and unwavering customer contentment.
- ISO 9001:2015, ISO 13485 Certified.
- 2,800,000 + quality parts produced
- Assured Excellence in Every Detail
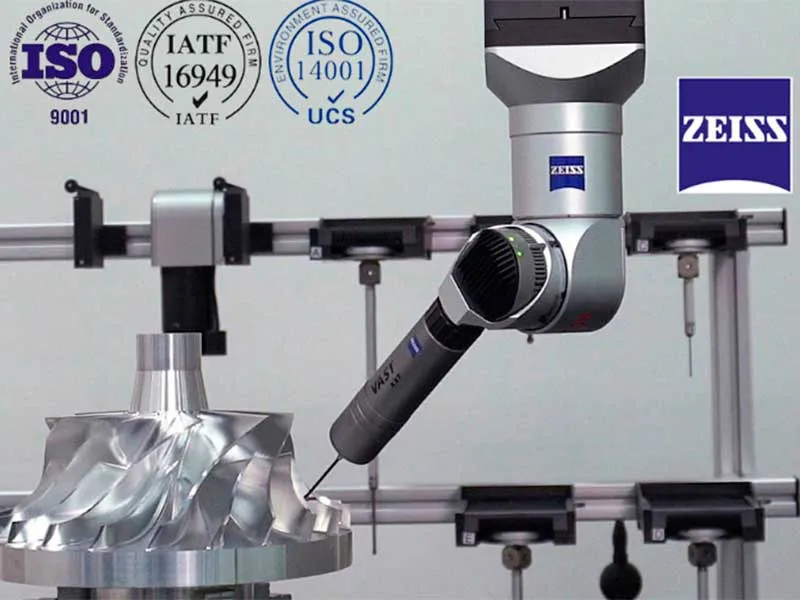
How Flagship Guarantees Superior Quality
Stringently Evaluated Partners
We approach supplier selection with utmost diligence, acknowledging their indispensable role in our operations. Consequently, we exert considerable effort to forge collaborations with industry-leading partners.
Quality Materials
We prioritize the quality of our materials, subjecting each incoming batch to a rigorous testing protocol. This meticulous examination enables us to discern premium materials from those of subpar quality, upholding our commitment to excellence in every aspect of our production
Experienced Project Engineer
Our team comprises adept project engineers devoted to scrutinizing and perfecting your project concepts. Armed with profound knowledge and expertise, they evaluate the practicality of your designs and devise the most efficient approach to craft the final prototype and production components
Exact Production
We’ve adopted a streamlined manufacturing process adhering to the ISO-2768-m and ISO-2768-c standards, meticulously crafted to achieve tight tolerances.
Thorough Inspection
We place a premium on thorough inspections across our production process. Our committed Quality Control (QC) team conducts an exhaustive range of examinations, encompassing material scrutiny, processing checks, and final product inspections.
Specific Practices for Quality Assurance
Technical assessment
Prior to commencing production, our engineering team conducts a comprehensive technical assessment of your parts design. This involves evaluating crucial factors like material, surface finish, structure, process, and other intricacies outlined in your 3D and 2D drawings.
Material verification
Upon customer request, we furnish a material certification for the components we manufacture. This report is sourced directly from the raw material manufacturer and typically encompasses details such as material heat number, grade, dimensions, mechanical properties, chemical analysis, and more.
On-site inspection system
In precision machining, maintaining precise material positioning is critical. Our on-site inspection system automatically scrutinizes positions, making real-time adjustments as needed. The implementation of this system not only averts early-stage issues but also contributes to cost and time savings.
In-process quality control
Adhering strictly to ISO9001:2015 standards at Flagship, our quality control team conducts regular inspections on all in-production parts every two hours. This proactive approach ensures ongoing quality and mitigates potential risks effectively.
Full-dimensional inspection report
Upon request, we furnish an exhaustive dimensional inspection report for every order. This detailed document covers key aspects, including part quantity, critical dimensions, threads and tolerances, thicknesses and depths, and overall part appearance, etc.
Packaging
Ensuring the superior quality of our manufactured parts is our top priority. Recognizing the inherent uncertainties in logistics, we take meticulous steps to minimize the risks during the packaging process. Our packaging protocol involves four layers of protection: 1. wrapping paper 2. EPE 3. foam 4. paper/wooden box, ensuring the delivery of parts that are not only of the highest quality but also aesthetically pleasing.
Quality Reports
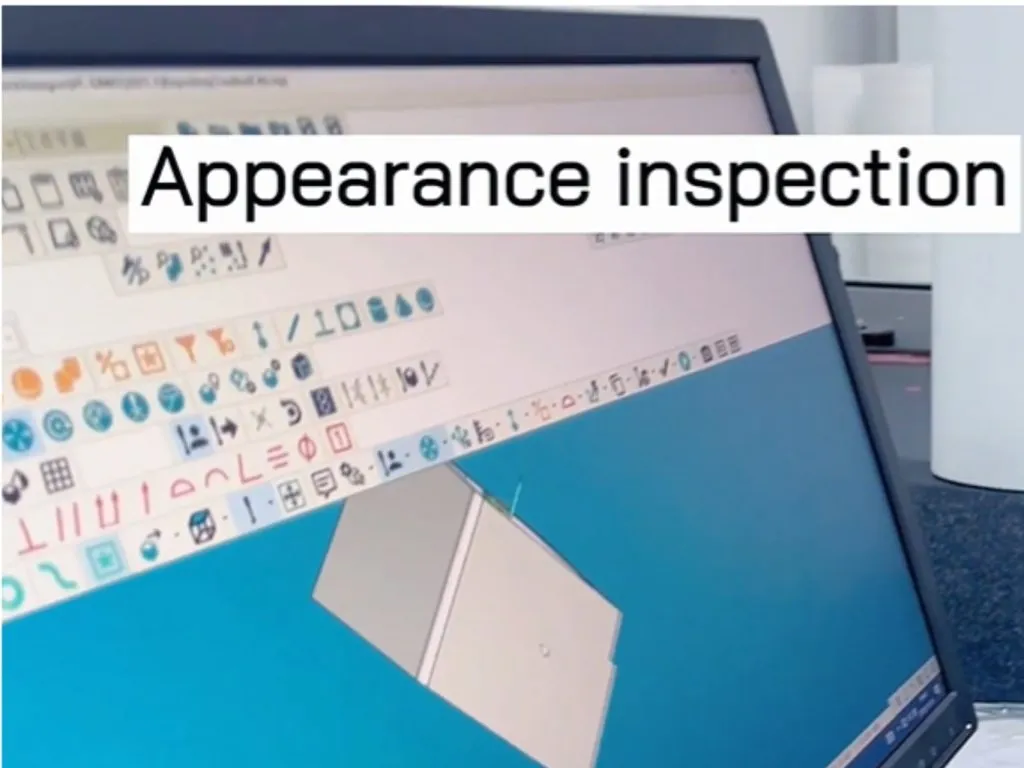
Visual Quality Inspection
At this phase, we validate adherence to the customer’s visual specifications for the product or part, taking into account aspects like color, texture, and other physical attributes.
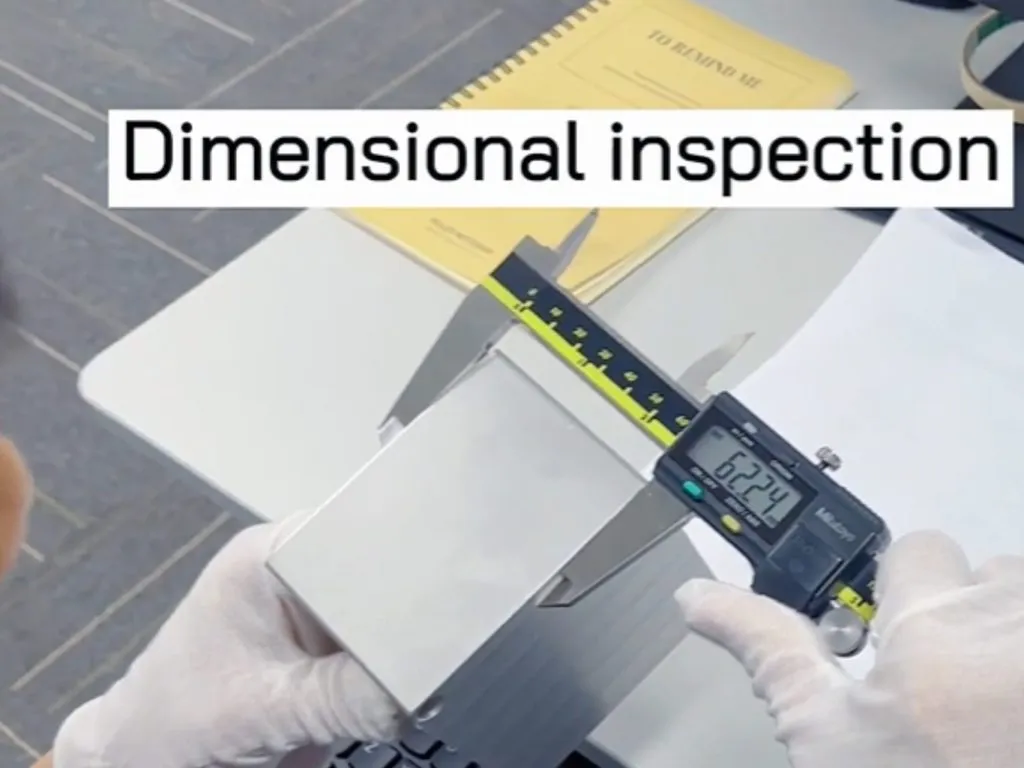
Precision Measurement
We inspect parts with straightforward designs utilizing vernier calipers, micro-calipers, and height gauges. For intricate products, we employ the CMM machine to ensure precise dimensional measurements.
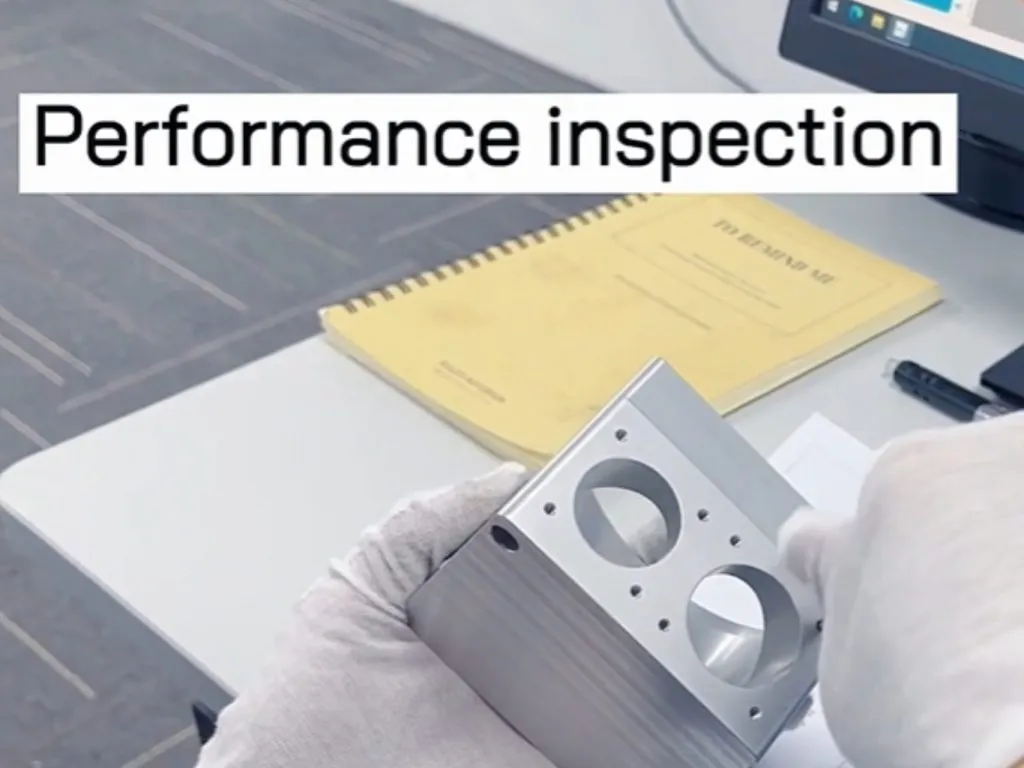
Performance Inspection
We conduct thorough examinations of the functionality and performance of the manufactured components. In the case of parts with threads or threaded holes, we meticulously inspect the assembly to guarantee precise fitting.
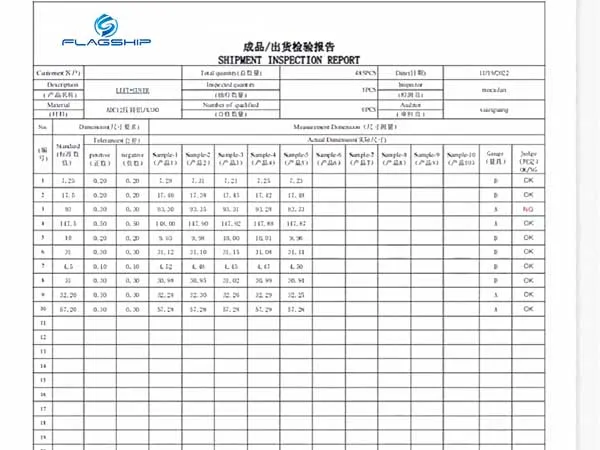
Initial Production Report
In the conclusive phase of the inspection protocol, we furnish our clients with the conclusive inspection report. This document provides a comprehensive summary of all inspection procedures and outcomes.
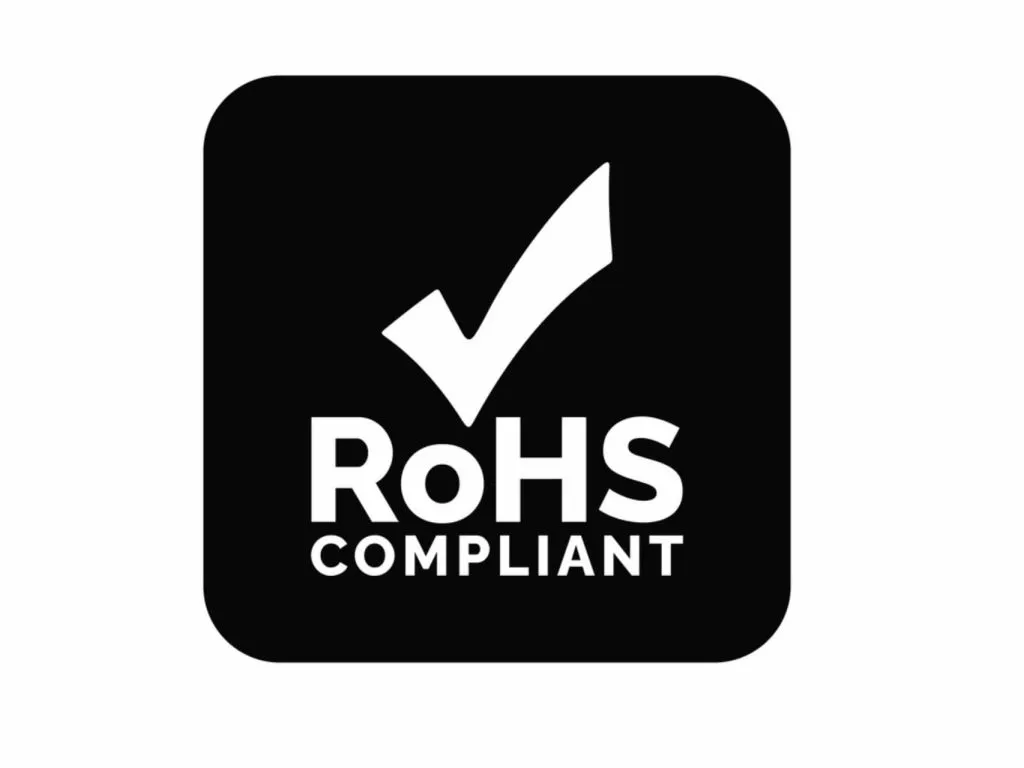
Material Certifications
Upon customer request, we offer a RoHS compliance report, validating adherence to the RoHS directive for a particular material or product.
Respond Quickly and Efficiently to Quality Issues
At Flagship, our goal is to provide outstanding prototypes and parts tailored to your precise needs. Should your order fall short of your specifications, we offer the option of rework or refund. Reach out to our specialists if any quality issues arise within one month of receiving your goods. Notify us of the matter within five business days from receipt, and we will promptly resolve it within 1 to 3 business days
Conditions for Rework
Upon notification of the issue, we conduct a thorough examination of the design and samples to identify any inconsistencies. Subsequently, we promptly address and rectify the concerns, ensuring swift dispatch of replacements.
- Unacceptable processing defects
- Fail to meet tolerance requirement
- Incorrect material / finish
Conditions for Refund
We promptly initiate the refund process upon verifying product issues and efficiently manage the return procedure
- The part is not machinable
- The customer does not agree to rework
- Other reasons
State-of-the-art Facilities
In our manufacturing facility, specialized workshops are outfitted with advanced equipment to conduct thorough inspections, facilitating the implementation of our rigorous quality control procedures
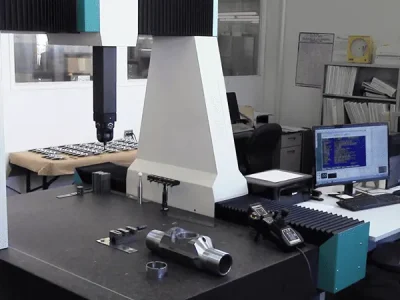
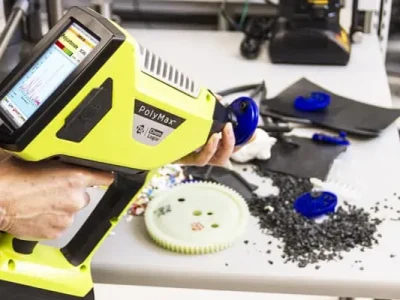
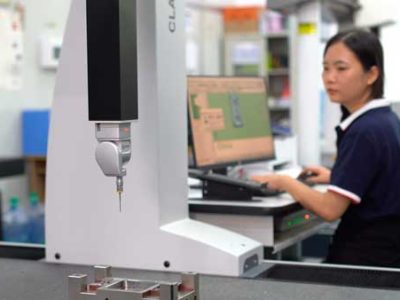
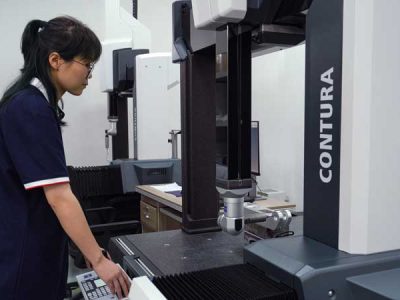
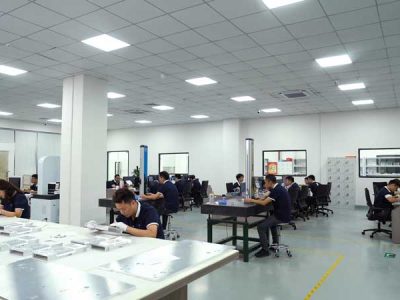

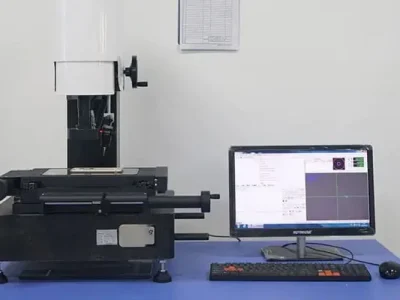
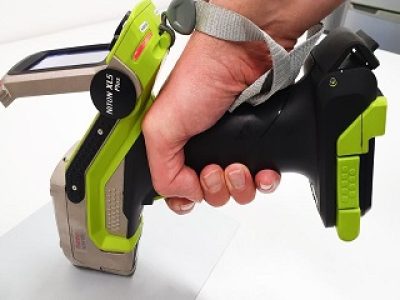
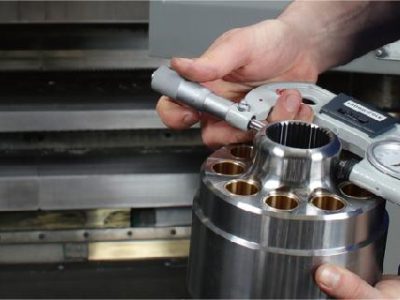
Contact
We Are Always Here for You
We have a team of skilled engineers ready to support you throughout your product development journey, from prototyping to production.
When you’re prepared to initiate your next project, just upload your design files, and our engineers will promptly provide you with a quote.
- 0086 755 2727 8919
- 0086 136 3168 1232
- 0086 135 3050 3436
- [email protected]